The high cost of passive fire protection, usually with the help of different painting systems, is an economic disadvantage of steel and composite structures compared to simple concrete constructions. If the corrosion protection system also protect from fire it would be of great benefit. Steel components are non-flammable and do not contribute to fire loads, but the mechanical properties of the steel are temperature dependent.
The calculated yield strength (above 400 °C) and the modulus of elasticity (above 200°C) decrease with an increasing temperature. For example, if a steel member reaches a temperature of about 600°C, about 53% of the initial strength is lost. This must be taken into account when dimensioning steel structures in case of fire.
Fire resistance
The fire resistance time is the minimum time in minutes that a structure will perform its function in a standard fire. The structure must therefore not collapse during this time. The minimum time is the basis for the classification according to Table 1. When a fire resistance of, for example, at least 30 minutes is required for a steel structure, it must be possible to ensure that the load-bearing parts of the structure still meet the static requirements during this time. High costs for passive fire protection can be avoided by determining the critical temperature for a specific structure according to Eurocode EN 1993-1-2.
Fire resistant class | Fire resistant time (Minutes) | Symbol in the construction inspection rules |
F 30 | ≥ 30 | Fire resistant |
F 60 | ≥ 60 | Fire resistant |
F 90 | ≥ 90 | Fire proof |
F 120 | ≥ 120 | Fire proof |
F 180 | ≥ 180 | Very fire proof |
Fire scenario and fire curve
A fire consists of several phases. Usually, the fire begins with a slow phase when the material ignites and smolders. Then comes the fire phase with a sudden flare-up that causes a substantial increase in temperature. The fire then goes out and the cooling phase begins. In real fires, each phase can vary greatly in terms of intensity and duration. In order to be able to compare the fire behavior of building materials, a temperature-time curve has been developed, which is included in the ISO 834 standard “Fire resistance tests – Elements of building construction”.
Structure of the zinc layer
When steel comes into contact with molten zinc, a reaction occurs between the metals so that an iron-zinc alloy is formed on the steel surface. This alloy is made up of different iron-zinc phases with decreasing iron content towards the surface. When the zinc is taken up from the molten zinc, a layer of pure zinc adheres to the outermost alloy phase, see Figure 1. The thickness of the coating and the appearance of the surface are determined by the reaction with the steel and how quickly the outer zinc layer solidifies. The course of the reaction depends on a number of parameters. Of these, the chemical composition of the steel is of greatest importance, but the condition of the steel surface (including structure, grain size, stresses and surface roughness) also plays a role. The composition and temperature of the molten zinc and the actual immersion time also have an effect.
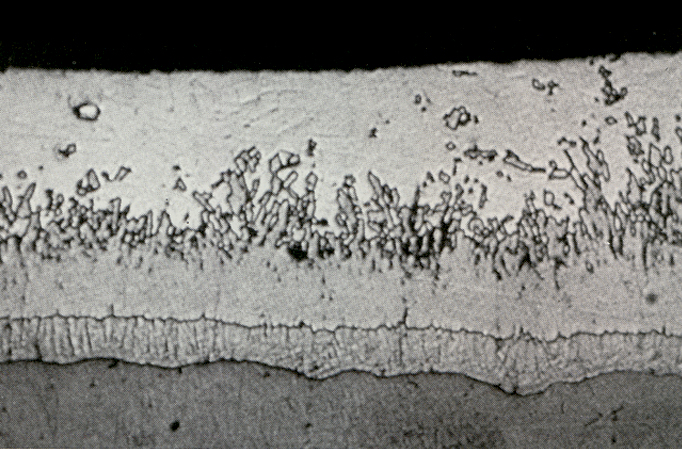
Several benefits with galvanized steel in fire
The results of practical tests with fire showed that the hot-dip galvanized steel had several advantages in comparison with the uncoated:
-Lower emission factor
-Slower heating
-Longer time until the critical temperature is reached
One important thing for the influence of the emission factor is the colour of the coating. To get a low emission factor like in the table above the coating should be bright or light grey. The zinc layer has a positive effect up to the steel reaching about 550 °C.
Type of steel | Emission factor up to 500 C | Emission factor over 500 C |
Carbon steel | 0,70 | 0,70 |
Stainless steel (1) | 0,40 | 0,40 |
HDG Steel (2) | 0,35 | 0,70 |
(1.) According to Annex C (2. )Steel galvanized according to EN ISO 1461 and with steel composition according to Category A or B of EN ISO 14713-2, Table 1.
Table 2. Emission factors for black steel, stainless steel and galvanized steel.
If the coating is dark grey the emission will be higher, so it is important to use the right type of steel. According to the foot note to the table above the steel should be aluminum killed, or silicon killed with a silicon content of maximum 0.25 %. To be on the safe side it might be better to recommend a little lower maximum Si- content, depending on the construction.
Interesting business case
The large business interest for fire protection with galvanizing could easily be understand from the picture below. If protection with paint is used there is demand for maintenance on a regular basis. With galvanizing no maintenance is needed and the intital costs are on the same level.
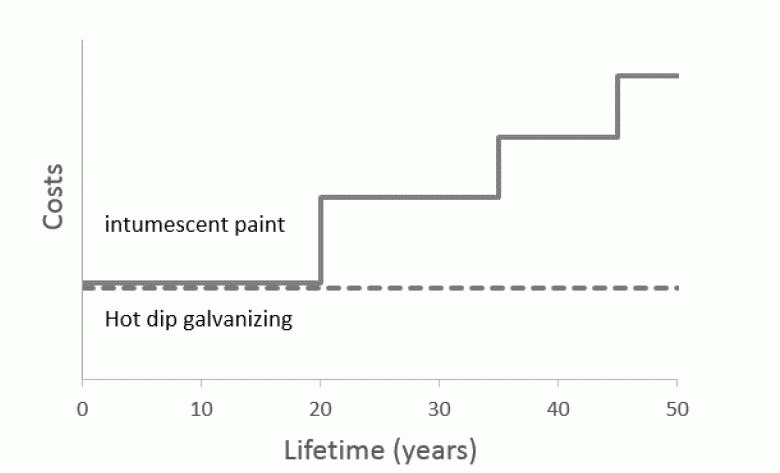
Implementation in Eurocode 3
Several countries in Europe have benefited from the improved fire resistance that hot-dip galvanizing provides for several years, and it has now also been implemented in Eurocode 3; EN 1993-1-2:2024 includes the table with new emissivity value for galvanized steel, see below
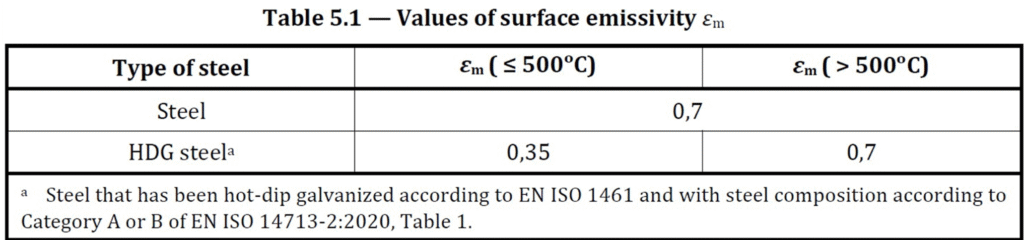
Summary
Studies have shown that the zinc layer has a positive effect on the heat generation during fire exposure. In many cases is it possible to withstand F30 in fire resistance of a hot-dip galvanized steel structure, without any additional fire protection. This means that the hot-dip galvanized construction can withstand 30 minutes of fire exposure according to the standard EN 13501-2 (Fire classification of construction products and building elements).