General
Design of structures to be hot-dip galvanized is no different from that for good structural, surface treatment and welding practice in general. However, certain components require special attention.
- It is important that larger structural components are matched to the size of the pickling tank and zinc bath (Fig 1). Sometimes “double dipping”, which involves the handling of structural components longer than the zinc bath, is employed. (Fig.2).
- Bolted joints are preferred instead of welding, since welding burns off the galvanized coating, which have to be repaired.
- The weight of the construction. The galvanizing plants can only handle constructions that the cranes can handle.
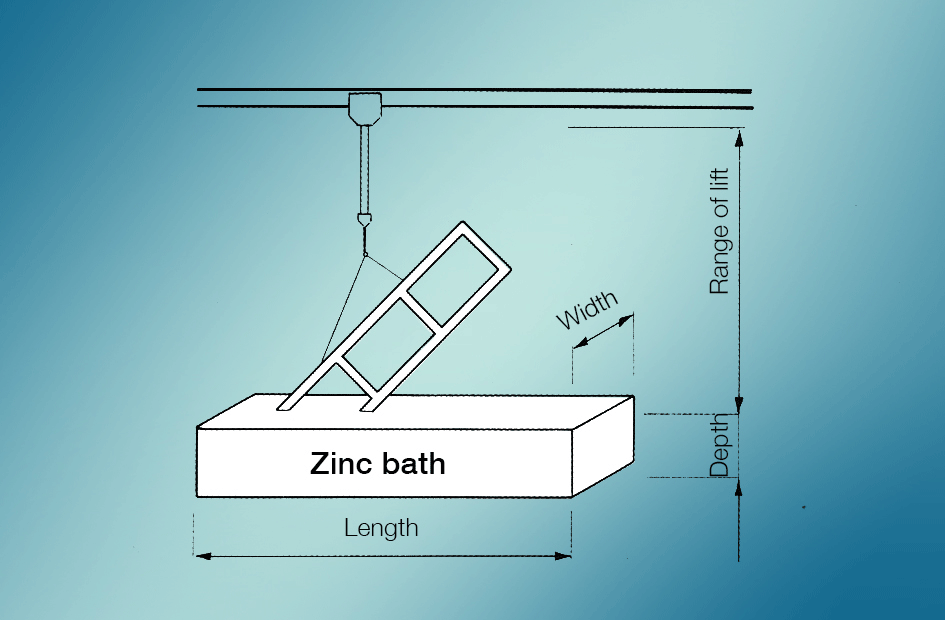
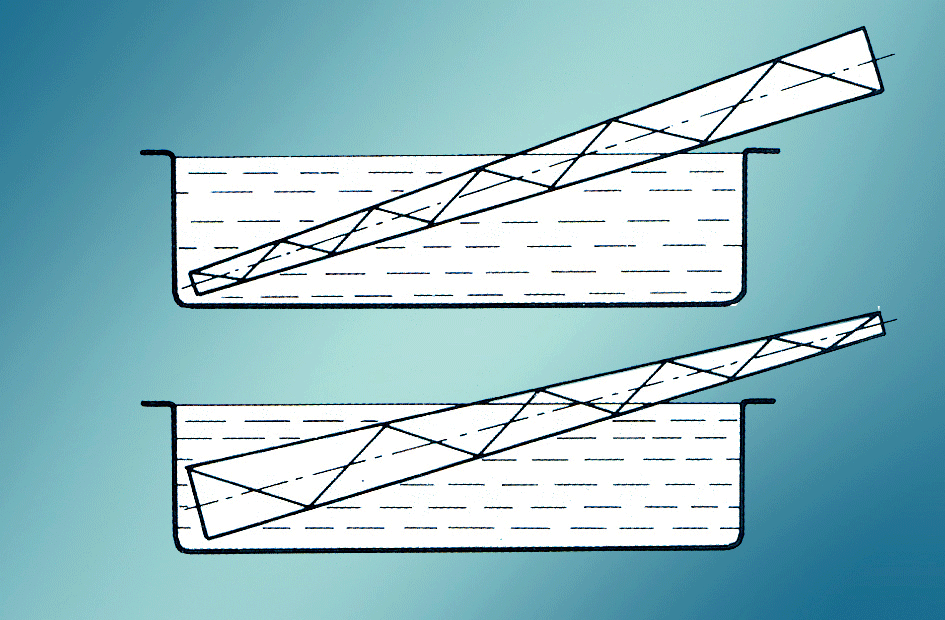
Clean steel surface
A pre-requisite for good results in hot-dip galvanizing is clean steel surfaces. One should therefore try to keep the surfaces free of paint, grease, oil and tar. Impurities such as these cannot be removed by pickling and result in black, uncoated spots after galvanizing. Surface contaminations in the form of grease, oil, tar, paint and welding slag require removal by means of degreasing, sandblasting or grinding. Contamination may be difficult to detect. If it becomes apparent after galvanizing the article may need to be regalvanized, which increases costs.Laser or flame cutting heats the steel and produces surfaces that react differently when galvanized. The coating thickness may be lower than expected and the adherence to the steel surface may be poor. The cut surfaces should therefore be ground to remove the heat affected zone before galvanizing.
Safety requirements
Hot-dip galvanizing involves dipping components and structures in both pretreatment baths and molten zinc. This means that hollow structures, such as pipes, tubing, and containers and also beam structures, which are welded round the connection point, must be provided with holes for drainage and venting. If a sufficient number of holes is not provided to enable complete venting, there is a significant risk that the structure will explode on immersion. Also, pickling acid is capable of penetrating pores in welds. Upon dipping in the zinc bath the residual pickling liquid is vaporized and the pressure can be so high that the object explodes. The risk of serious injury to personnel, or damage to materials, is great when such explosions occur.
Suitable dimensions for venting holes are given in table 1. The holes must be located to enable total venting and to enable pickling acid and molten zinc to run in and out easily. Illustrations show this point. Examples of the location of the holes are given in the illustrations. It is also advisable to contact the galvanizer to discuss alternative hole sizes and locations. Holes can be formed by drilling, grinding or gascutting.

Design considerations
The following guidelines are not necessarily preconditions for hot-dip galvanizing but, if they are observed, quality is likely to be considerably better and the galvanizing process easier.
Provision for handling
A structure should preferably be designed with easily handled components, which are assembled after hot-dip galvanizing. Threaded unions are a good means of achieving this. The structure or object should be equipped with lifting holes or lifting eyes, to which lifting gear can be connected. Avoid inwardprojecting pipe connecting stubs in containers. Pipe connecting stubs should be located in corners and diagonally, otherwise the container cannot be completely emptied of zinc (fig.4).
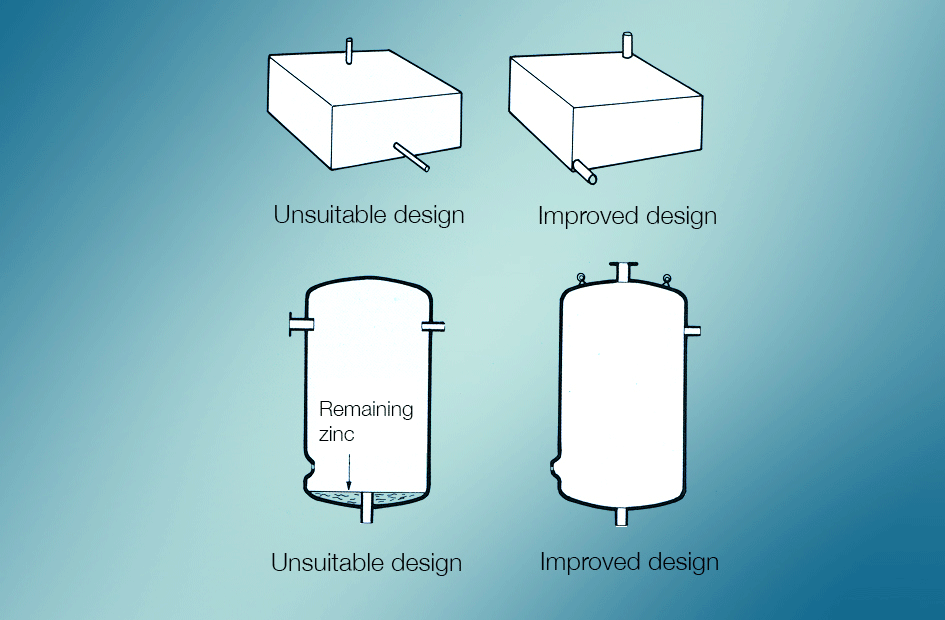
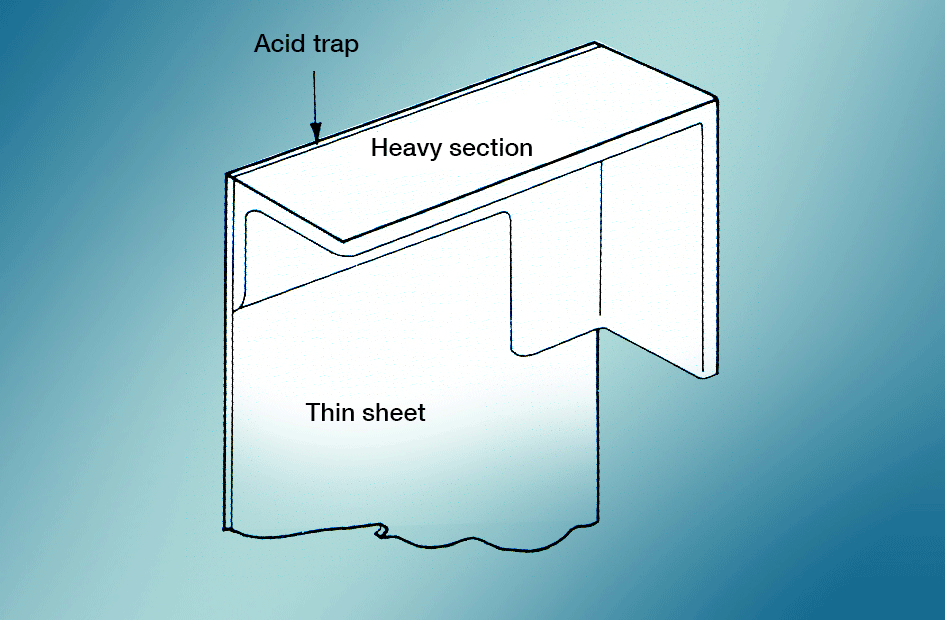
Mobility
Components that are to move on each other should be assembled after hot-dip galvanizing. If this is not possible, mobility can be retained by giving the components a clearance of 1.0 mm on each side, i.e 2.0 mm larger than the shaft.
Avoid structures that can distort
Materials with excessive variation in sectional thickness should not be combined on the same structure or object (fig. 5). Otherwise, heating in the zinc bath would be uneven, and the object could warp. Long, slim structures should be avoided. Large flat sheet surfaces, where the sheet thickness is less than 3—4 mm should be stiffened (fig.6), or they might warp.
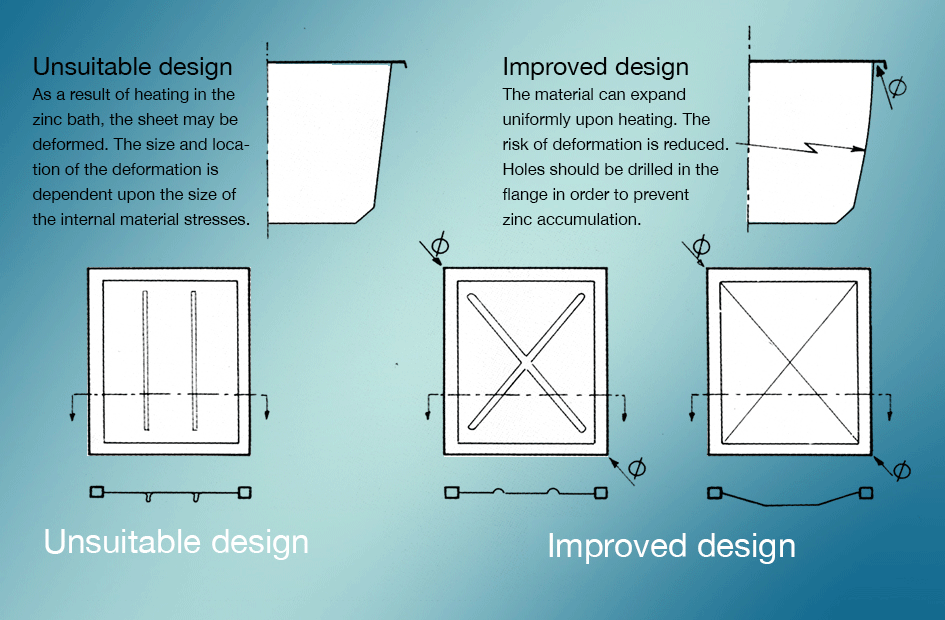
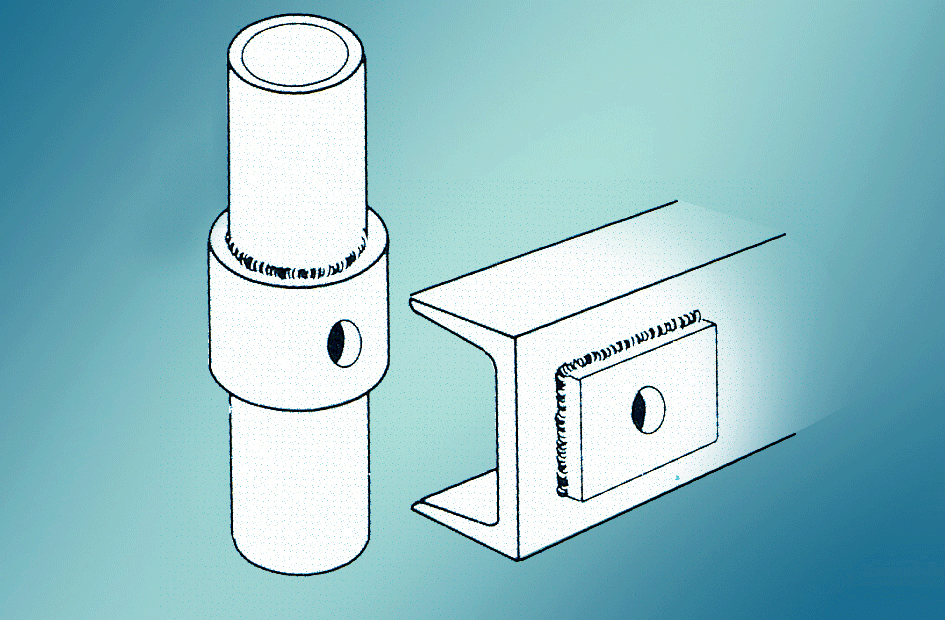
If possible, structures should be designed so that welding can be performed symmetrically, around an axis of flexure. The welding sequence should be planned so that stresses are as low as possible.
Avoid combining different materials and different surface conditions
Newly rolled steel should not be welded to cast iron, or to steel that has been attacked by deep-seated rust, since the zinc coating will be uneven and the appearances of the surfaces will be different. Such materials must be galvanized in different ways, which is not possible if they have been welded together.
Different types of steel, such as rimming or aluminium killed steel, should not be welded to silicon-killed steel. If this is not observed, both the appearance of the surface and the thickness of the zinc coatings will be different.
Avoid acid traps
Structures should be designed to avoid narrow crevices or gaps (fig. 9 and 11). As far as hot-dip galvanizing is concerned, butt welds are better than lap welds. If lap welds must be used, they should be welded around the entire joint. It is important to avoid the formation of pinholes. If the gap between contact surfaces is greater than 100 cm2, venting holes must be provided to avoid the risk of explosion (fig.7).
If acid has penetrated a crevice, it cannot be removed later. Since molten zinc is more viscous than acid, it will seal the opening during hot-dip galvanizing. After a while, the acid causes holes in the coating over the opening. A rust-coloured liquid then runs on to the surface and spoils the appearance. Corrosion in such crevices can become so severe that the connection eventually fails.
Castings should have an even, sealed and sand-free surface. Pores and cavities can act as acid traps and should therefore be avoided.
Avoid pockets
Structures should if possible be designed so that the zinc can run freely off all surfaces when the object is withdrawn from the zinc bath (fig.8). The coating will otherwise be uneven.
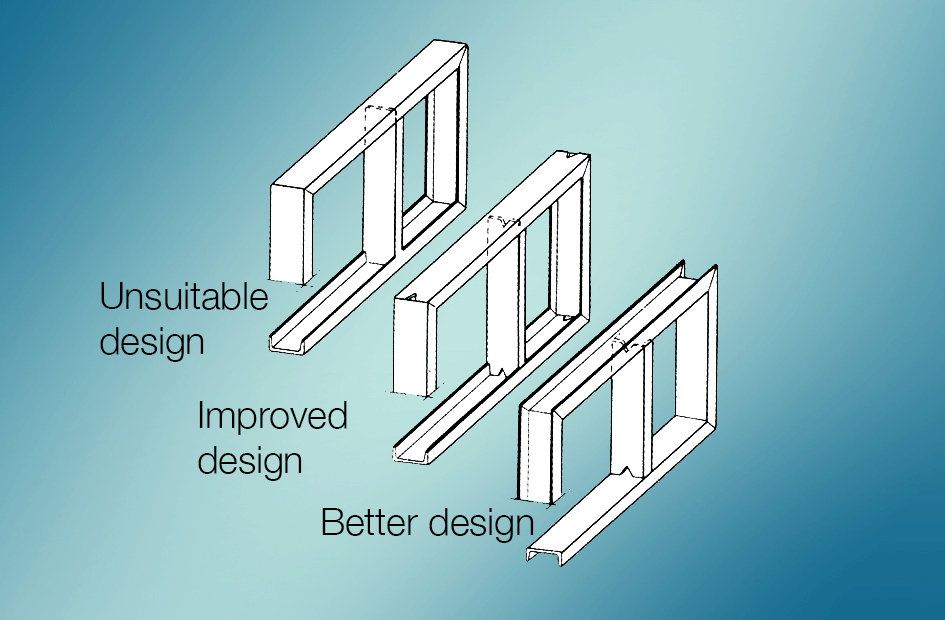
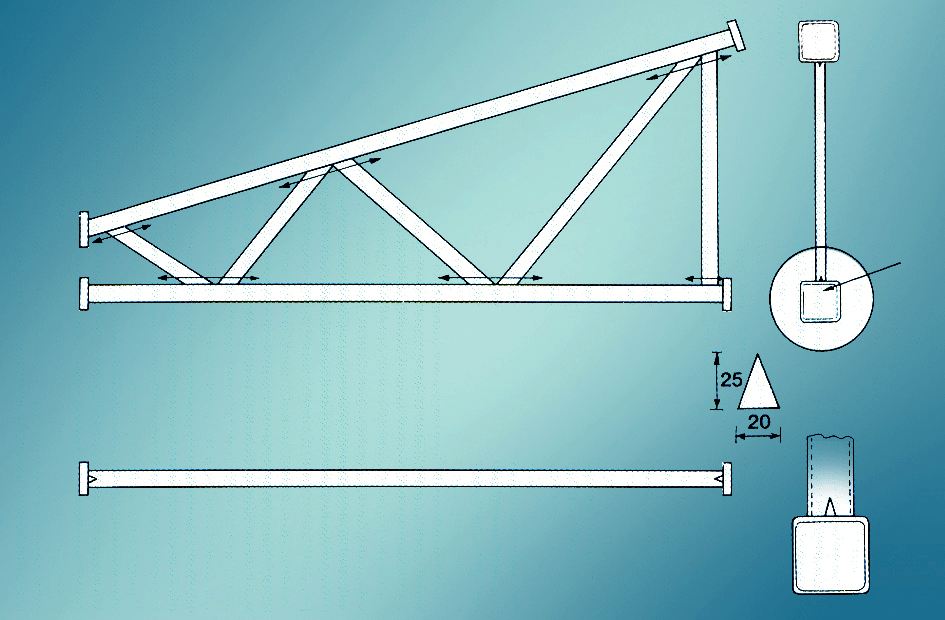
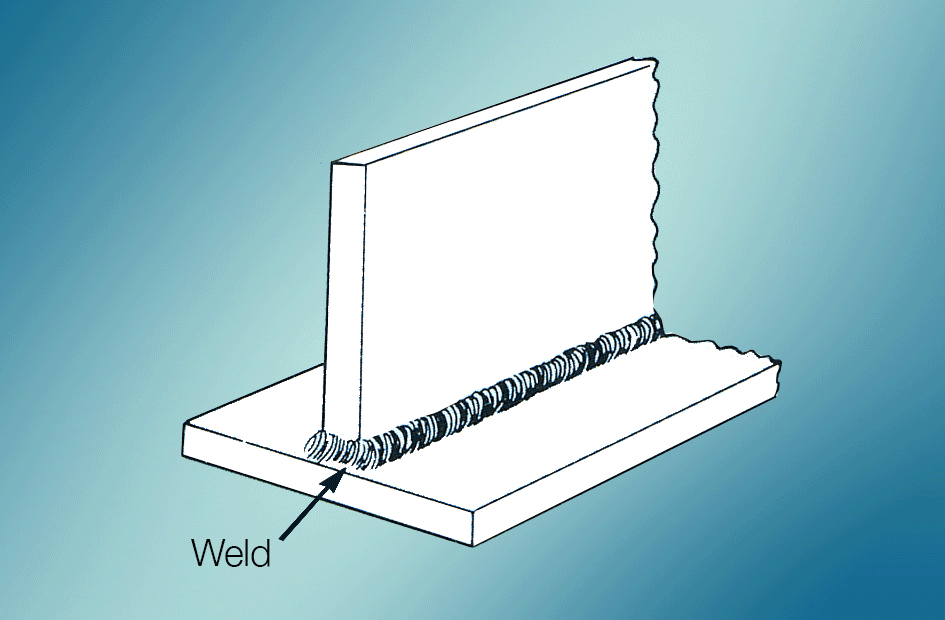

Components that are to move on each other should be assembled after hot-dip galvanizing. If this is not possible, mobility can be retained by giving the components a clearance of 1.0 mm on each side, i.e 2.0 mm larger than the shaft.
Threaded objects
Male threads must be cut undersize to enable them to fit the respective nuts after galvanizing. Suitable reduction of the thread diameter is given in standards. Female threads are cut or cleaned to nominal size after galvanizing. Male threads in assembled structures must be cleaned after galvanizing. The zinc coating on male threads also protects the steel in female threads.
Marking
Temporary marking of steel to be hot-dip galvanized should be carried out with water-soluble paint only. Permanent marking can be done by stamping letters or numbers on the object, or to an attached ID plate. Stamping should be to sufficient depth to enable the marking to be read even after galvanizing.
Welding
Welds should be free of pores, which could act as acid traps. In case of double-sided fillet welds, the weld must be continued over the ends of the sheet to prevent the penetration of acid into any conceivable crevice (fig.9).
Welding methods which do not produce slag, such as MIG welding, are preferable. If coated welding electrodes are used, all slag deposits should be carefully removed from the weld. It is not possible to remove welding slag through normal pickling, and any residue causes the formation of black spots during hot-dip galvanizing.