Batch galvanizing
In batch galvanizing, the steel structures are dipped into a bath of molten zinc and a chemical reaction between the steel and the zinc takes place. An alloy layer is built up, which ensures a very good adhesion. The protective layer is formed on all surfaces of the structure, both external and internal. The layer has a very good durability and gives the construction a greatly increased lifespan. The layer thickness is controlled by the choice of steel and immersion time, and is usually in the range 55–215 µm. Coatings formed by this process are allowed to use the quality mark in Figure 1, which shows that the coating is formed in accordance with the standard EN ISO 1461.
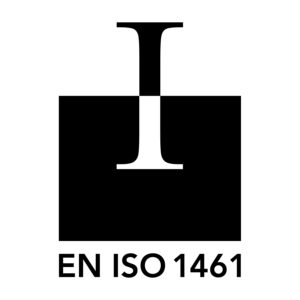
Continuous galvanizing of steel sheet
In the continuous process, a thin plate passes through a zinc bath and a layer is built up on the steel, which is later used to make products. The zinc bath can either consist of essentially pure zinc with very small alloying additions, or be alloyed with higher concentrations of other substances, such as aluminum.
ZM-steel
In recent years, there has been an increase in continuously galvanized materials in baths which, in addition to zinc, contain around 3.5% aluminum and 3% magnesium. These are generally referred to as ZM steel and are sold under various brand names. Since the coating in the continuous process is applied before manufacturing the products, the layer must withstand a certain deformation, which can be a problem if it is alloyed with substances that form brittle intermetallic phases in the coating. In addition, all cutting areas and cutting edges are uncoated, without a protective layer, on such a product.
Self-healing effect
It is often talked about that zinc as a corrosion protection has the advantage of providing cathodic protection in the event of damage to the zinc layer, an advantage that we often see working well for minor damage on a batch galvanized product. In that case, there is plenty of zinc available on the product because the layer thickness is high and the area that needs to be protected is also limited in size. However, to trust the protection of all cut edges and holes of a continuously coated product entirely on the self-healing effect is more questionable. For the self-healing effect, which is based on galvanic corrosion, to work, a certain corrosiveness of the environment in which the product is used is required. In a less corrosive environment, no passive layer is built up in a reasonable time, and red rust is found on the uncoated surfaces, figure 2. If, on the other hand, the environment is more aggressive, the galvanic corrosion occurs as expected but at the expense of the protection of the sheet metal surface near the uncoated areas, which causes these to be depleted of zinc and begin to corrode.
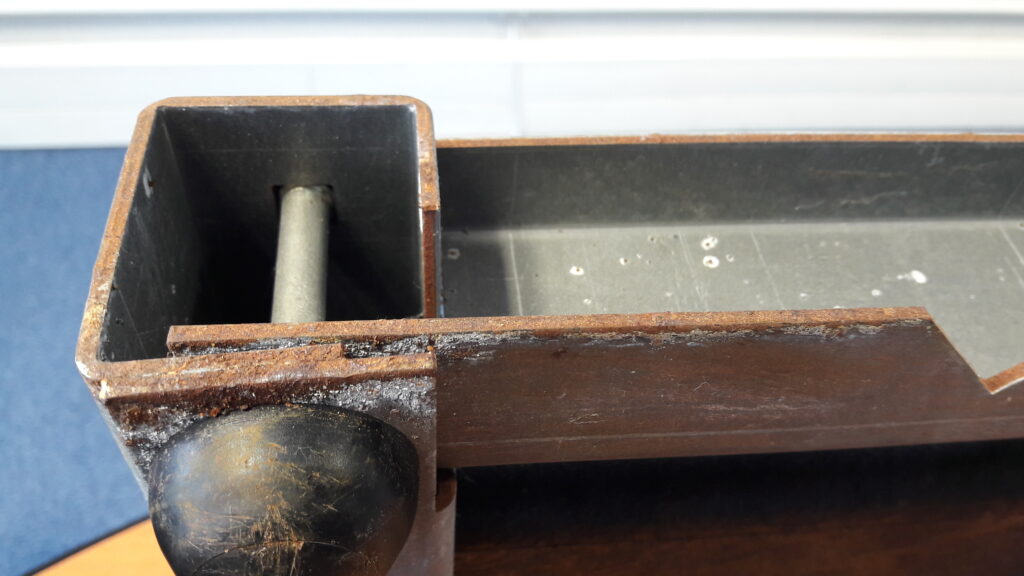
Accelerated Corrosion Testing
The corrosion properties of ZM steels are often reported based on results from accelerated corrosion testing, usually in salt spray. Materials tested using this method are placed in a temperature-controlled chamber where a saline solution at 35°C is sprayed as a very fine mist.
Since the spraying is continuous, the samples are constantly wet, without cyclical drying. The samples are therefore constantly exposed to corrosion, which does not occur in reality, and prevents metals such as zinc from forming a protective passive film, as is the case with real exposure.
Due to the addition of magnesium in ZM steels, they show greater resistance to this artificial exposure, something that has been used in marketing them as “better than hot-dip galvanized steel”, and which would justify that they provide equivalent or better protection despite the low layer thickness.
Real full-scale studies
In a commission for the infrastructure project “Stockholm Bypass”, the research institute RISE assisted the Swedish Transport Administration with the development of corrosion-related requirements for materials and coatings for use in road tunnels. In this study, test panels made of different materials were installed in a number of road tunnels, which are considered to be an aggressive environment for most metals and surface coatings.
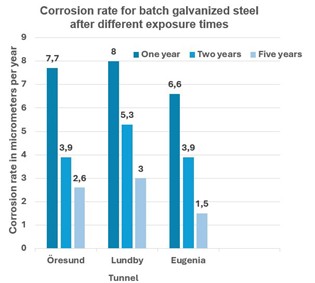
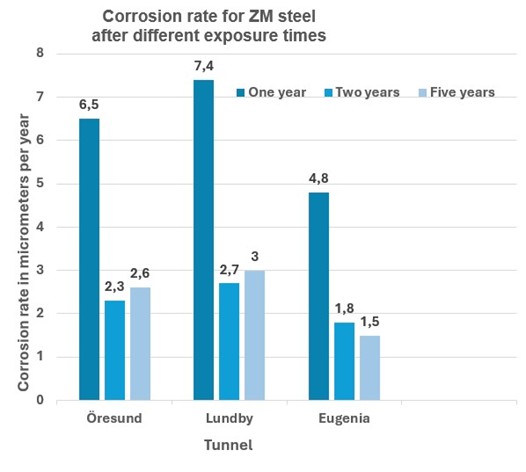
Samples were taken for analysis after 1, 2 and 5 years. As can be seen in the diagrams above, these tests did not show any major difference in corrosion rate for batch galvanized and ZM-coated steel. The batch galvanized steel has slightly higher corrosion losses initially, before the protective patina has had time to build up, but after 5 years of exposure the corrosion rate is the same for both materials and the expected service life will therefore be given by the thickness of the layers, as shown in the table below.
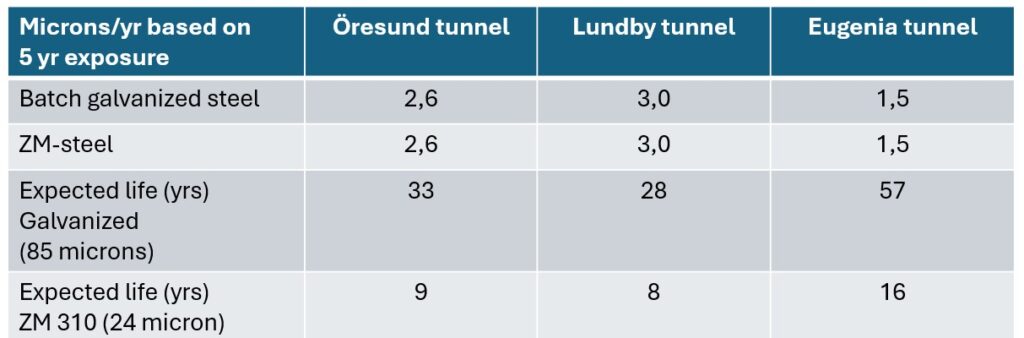
service life of hot-dip galvanized and ZM-coated steel (1).
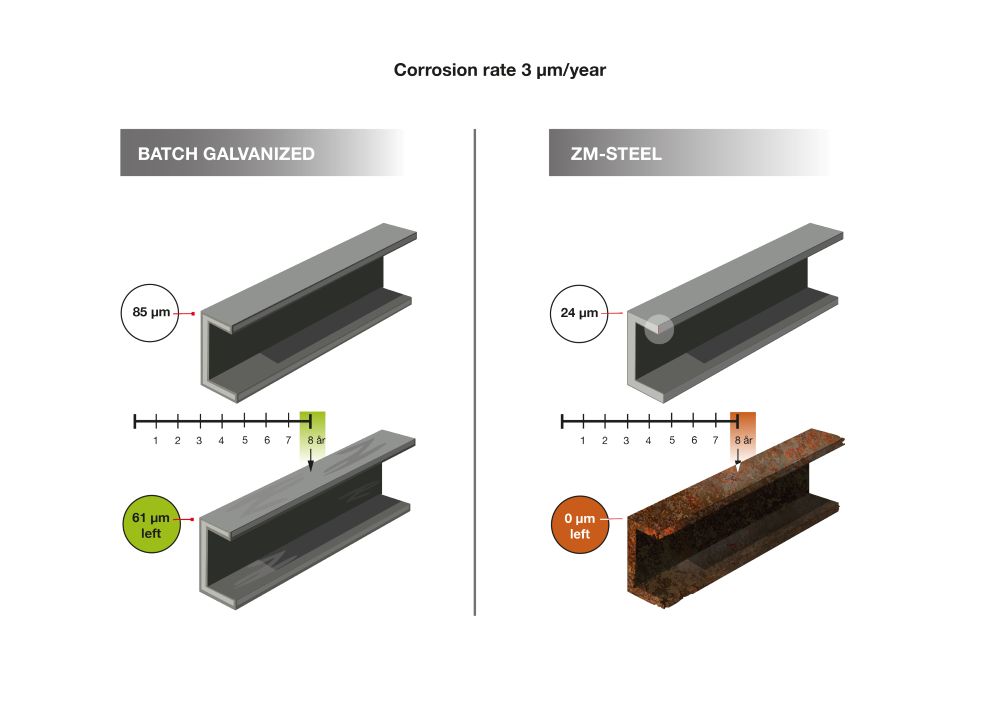
Forming
The forming of the ZM-coated steels that takes place during product manufacturing also has certain limitations. ZM coatings currently offer poorer formability compared to pre-coated sheet metal where the layer consists solely of zinc. This is because the brittle phases in the ZM coating can lead to cracking in heavily deformed areas.
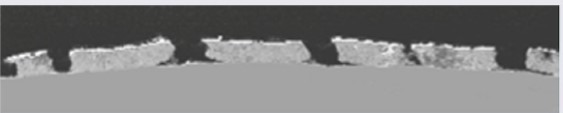
surface treatment, there is a risk of cracks in the ZM layer.
Some of all the advantages with batch galvanized steel:
Batch galvanizing provides a well-proven corrosion protection where there is a large amount of reliable data from exposures in many different types of environments over very long periods of time. These results are significantly more informative than those from accelerated testing which do not reflect real-world conditions.
Batch galvanizing provides complete coverage, both externally and internally, on all surfaces of a structure.
Batch galvanizing provides cathodic protection in minor damage, meaning that repair is not needed.
Batch galvanizing provides the opportunity to coat everything from small fasteners to large, heavy structures.
Batch galvanizing provides a durable, abrasion-resistant layer.
Batch galvanized steel is robust and can be dismantled, stored and then used in new constructions.
Batch galvanized steel can be galvanized again when the original layer has been consumed, so-called remaking, which is increasingly requested in the circular economy.
When recycling a hot-dip galvanized construction, zinc and steel are recovered in the same process.
(1) References:
EGGA, “The Importance of the Correct Specification of Metallic Coatings for Steel” White Paper 2024, J. Engblom, B.Sederholm “Recommendations for material selection in tunnel environments – Final report” KIMAB – 2020 – 12408-6, L. Sjögren, J. Engblom and B. Sederholm, “Inspection of tunnels as a basis for corrosion-related material requirements for the Stockholm Bypass” – Swerea KIMAB 12371:2”.
Read more here:
A summary of the document above could be found here: