Batch galvanizing
In bach galvanizing, the steel components are first degreased and pickled and then rinsed with water. They are then dipped in a flux solution of aqueous zinc-ammonium chloride and dried befor dipping into the molten zinc bath.
When clean steel is immersed into molten zinc, a series of zinc-iron alloy layers are formed by a metallurgical reaction between the iron and zinc, providing a robust coating which is an integral part of the steel.
Batch galvanizing offers coverage both of the finished product externally and internally within hollow sections, it self-repairs when damaged, sacrifices itself to protect the base metal, is environmentally sustainable, has good impact and abrasion-resistance and a maintenance-free life of 50 years or more.
The coating thickness depends primary on the chemical composition of the steel, the surface roughness and the dipping time into the molten zinc bath. The coating thickness wary between around 50 to 220 microns. Also higher thicknesses are possible but the risk for brittle coatings increase with increasing thickness over a certain level and should be used with some caution.
One large benefit with batch galvanizing is that the dipping process of the finished product secure that all surfaces have the same coating and there are no unprotected, cut edges, holes or internal surfaces without a galvanized coating.
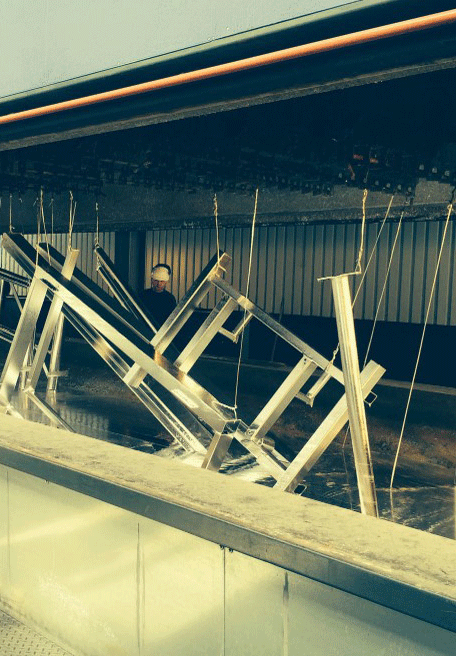
Sheet galvanizing
Steel sheet is hot-dip galvanized in continuous production lines in which all the processes are linked together. The base material consists of cold-rolled sheet in coils. One coil is welded to another to form a continuous strip.
After degreasing, the strip is pickled or oxidized. Oxides are then removed from the surfaces by reduction at 950 °C. At the same time the strip is soft-annealed. The surfaces of the strip, now chemically clean, are moved through a protective gas atmosphere and directly into the zinc bath. The dipping time is short, after a few seconds the strip is withdrawn from the bath vertically and passed through “air knives”. Fine jets of air or steam are blown through the knives, wiping the zinc coating to the desired thickness. Control over the knives and the thickness of the coating is achieved with the aid of thickness gauges and computer control. After cooling, straightening and treatment against wet storage stain, the strip is cut into suitably sized sheets or rolled into coils for delivery.
Thin sheet is galvanized with micro alloyed, low-alloyed or high-alloyed zinc. The most important alloy additive is in all cases aluminium. Typical contents for the aluminium additions are 0.2% for micro alloyed, 5% for low-alloyed and 55% for high-alloyed. There are many trade names for these products, such as Galfan for the low-alloy type, and Aluzink or Galvalume for the high-alloy type. There are also products on the market called ZM-steel, which is thin sheet steel galvanized in an alloy of aluminium, magnesium and zinc. The coating thickness is normally between 7-25 microns. Cutted edges will be unprotected and the lower coating thicknesses make galvanized thin sheet steel usable in less corrosive environments.