Steel is the most common material in use today. However, steel have one large disadvantage – its high corrosion rate. The protection of steel structures and components is therefore of great economic importance.
The best corrosion protection for steel is obtained with zinc. Zinc coatings on steel protect against corrosion in two ways:
- By a barrier effect, i.e. they prevent oxygen and moisture from reaching the steel surface.
- By giving cathodic protection at scratches, chips, edges etc.
Zinc is a metal with a relatively low galvanic potential and a high tendency to corrode. However, the corrosion rate is low in most environments, since the surface of the coating is quickly covered with corrosion products, which subsequently protect against further corrosion.
Corrosion in the atmosphere
When a hot-dip galvanized object leaves the zinc bath the surface of the object is immediately attacked by oxygen in the air. The resultant oxide layer has very little ability to protect against corrosion. However, water and carbon dioxide in the air quickly change the oxide layer to zinc carbonates. These give a sealed layer with very good adhesion. Since the carbonates have very low solubility in water they give excellent protection to the surface of the zinc coating. The original shiny surface with a metallic lustre disappears to be replaced by matt, light grey colour (fig.1).
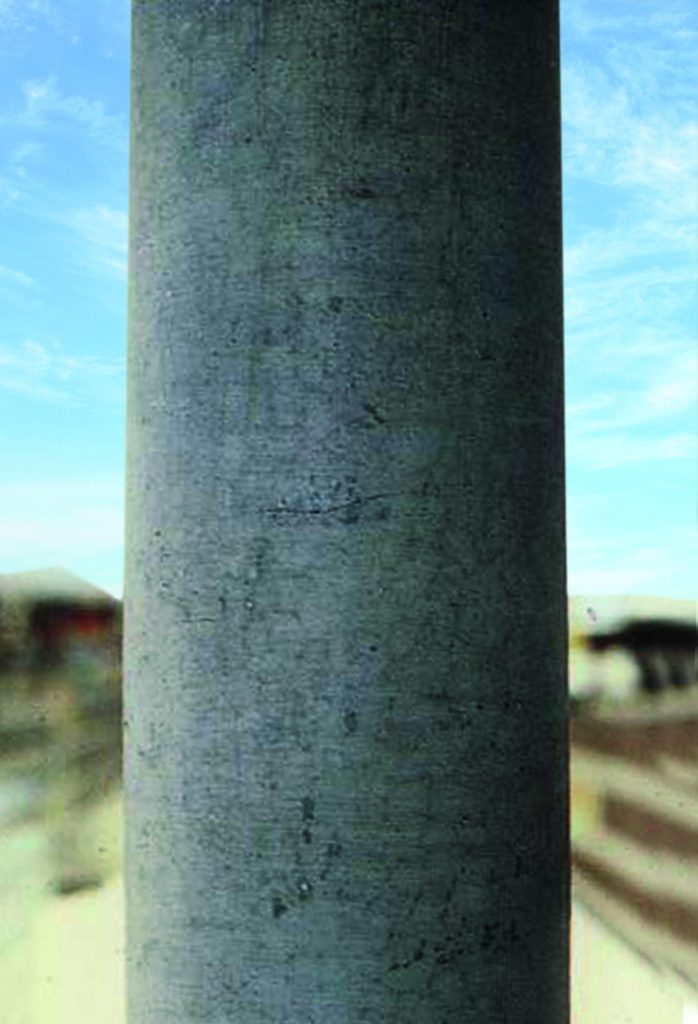
Fig 1. Exposed surface of a zinc coating with outer layer of pure zinc. The shiny surface disappears to be replaced by grey corrosion products (sometimes called zinc patina).
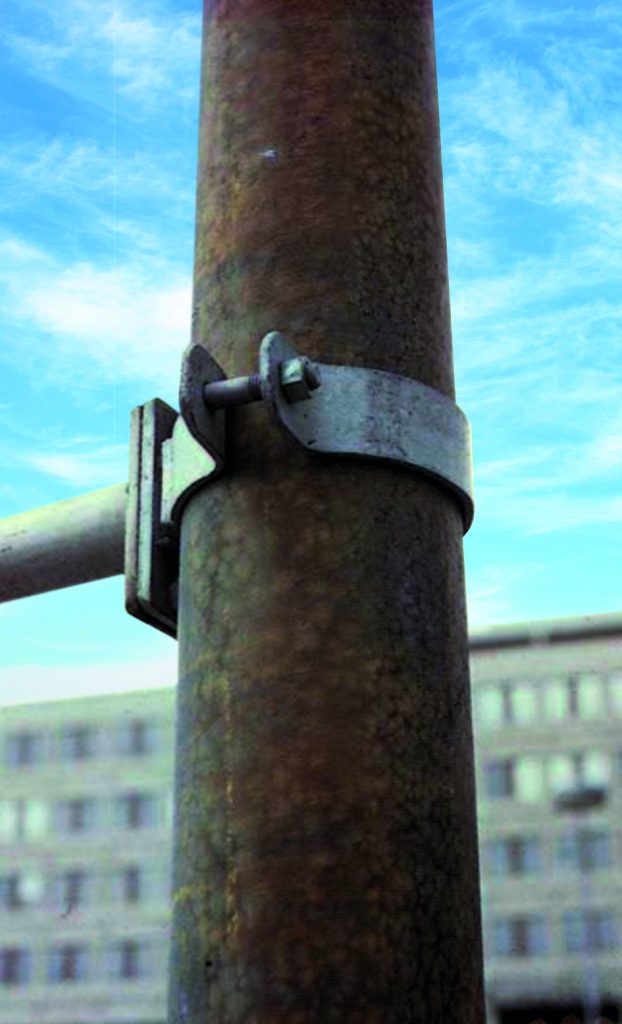
Fig. 2. Discoloured surface on lighting column. Coating consists mainly of an iron-zinc alloy that extends to the surface. Iron is exposed during corrosion, which leads to rust formation. It is only surface rust and is of aesthetic significance only.
Outdoor air contains greater or lesser amount of corrosive elements — gases, soot, humidity (fog, dew, rain, snow), inert and aggressive dust. Levels can vary with location and the time of the year. Sulphates and sulphites of zinc are water soluble and have poor adhesion to the zinc surface. They are therefore washed away easily by rain. A fresh zinc surface is then exposed to attack by oxygen in the air and the corrosion cycle is repeated. Corrosion in air containing sulphur oxides is therefore greater than in clean air. However, the amount of sulphur dioxide in the atmosphere has decreased drastically during recent years, and consequently zinc corrosion has also decreased.
In marine environments, the corrosion of zinc is influenced by the salt content of the air. However, marine air contains small quantities of magnesium salts, with good passivating influences. Corrosion is therefore not as great as might be expected. The salt content of the air reduces quickly away from the coast.
The corrosion of zinc is influenced by many factors. This means that a generally applicable formula for corrosion rates cannot be given. Zinc coatings have, however, been used for a long time, under a wide range of conditions, to protect steel from rust. A large number of long-term tests have also been conducted. Knowledge about the corrosion of zinc and corrosion rates in different environments is therefore good. Today, there are examples of zinc coatings that have been exposed for more than one hundred years.
The colour of corrosion products varies according to the environment in which they are formed. Marine environments give somewhat whiter corrosion products compared with rural and urban environments. Corrosion products are usually darkest in urban environments.
Corrosion in liquids
The zinc surface is generally covered with a protective layer of corrosion products when it is submerged in a liquid. However, liquids can be acidic or alkaline and can contain dissolved or solid particles of aggressive substances. The temperature and flow rate of the liquid are also of significance. All this means that the protective layer can have a highly varying composition or may not form at all.
Electro-chemical corrosion, which plays a subordinate role in air, is of greater significance in liquids. The extent of electro-chemical corrosion depends on the electrical conductivity of the liquid, which affects the protective influence of the zinc layer over greater or smaller areas.
The pH value of the liquid is of most significance. The corrosion rate of zinc is normally low and stable in the pH range of 5,5—12,5, at temperatures between 0 and 20 °C. Corrosion outside this range is usually more rapid.
Hard water, which contains lime and magnesium, is less aggressive than soft water. Together with carbon dioxide these substances form sparingly soluble carbonates on the zinc surface, protecting the zinc against further corrosion.
Soft water often attacks zinc, since the absence of salts means that the protective layer cannot be formed.
Aggressive soft waters can be found in many rivers and lakes in Finland, Norway, Sweden and similar environments.
If the flow rate is greater than 0.5 m/s the formation of the protective layer on the zinc surface is inhibited and corrosion accelerates.
Water temperature is of great significance to the rate of corrosion. Above approximately 55 °C, the layer-forming corrosion products acquire a coarse-grained structure and lose adhesion to the zinc surface. They are easily dislodged and expose new, fresh zinc for continued and rapid corrosion attack. The rate of corrosion reaches a maximum at about 70 °C, after which it declines so that at 100 °C it is about the same as at 50 °C.
The corrosion sequence in water is very complex and is influenced heavily by very small variations in the composition of the water. It is therefore difficult to give generally applicable rules. The informaton in figure 3 is based on practical experience and gives guidelines for some different types of water.
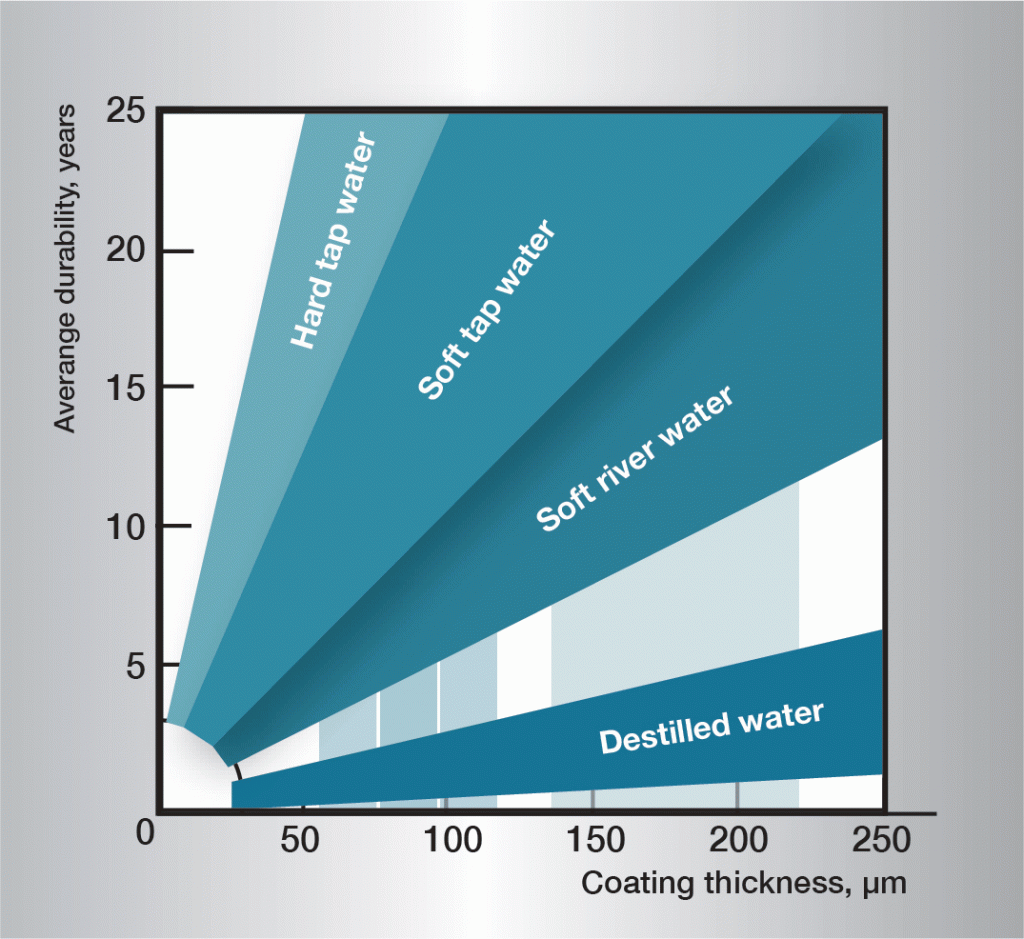
Fig. 3. Service life in different waters.
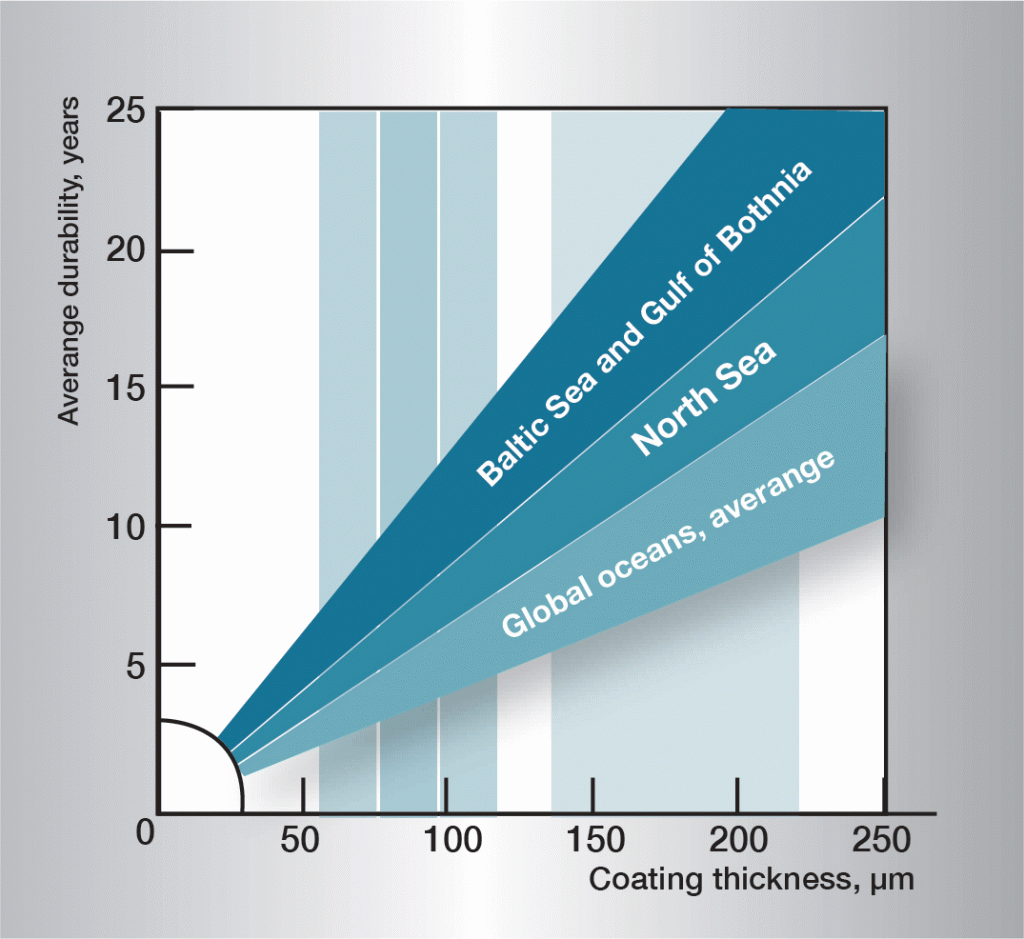
Wet-storage stain
Sometimes a white, floury and voluminous layer called wet-storage stain, or white rust, appears on galvanized surfaces (fig.4). White rust forms on materials with newly galvanized, shiny surfaces and especially in crevices between closely packed sheets, angle-iron and similar materials. A pre condition is that the material is exposed to condensation or rain water in conditions where the moisture cannot evaporate quickly. Zinc surfaces that have already received a normal protective layer of corrosion products are seldom attacked. When zinc coatings are exposed to air, zinc oxide and zinc hydroxide are formed. Under the influence of carbon dioxide in the air these are converted to basic zinc carbonates. If air access to the zinc surface is restricted, as in narrow crevices, then the area receives insufficient carbon dioxide to enable the normal layer of carbonates to form.
The wet-storage stain layer is voluminous and porous and only loosely attached to the zinc surface. As a result, protection against continued attack does not exist. Corrosion can therefore continue as long as moisture remains on the surfaces. When wet-storage stain has occurred, the object should be stacked to enable the surfaces to dry quickly. This will stop the attack and, with free access to air, the normal protective layer will be formed. The wet-storage stain is gradually washed away and the coating acquires an appearance that is normal for exposed, hot-dip galvanized steel.
Since this white corrosion product is very bulky (about 500 times that of the zinc from which it was formed), it can appear to be serious. However, wet-storage stain often has little or no significance on the service life of the corrosion protection. In the case of very thin coatings however, e.g. on electroplated objects, a severe attack of wet-storage stain can be of significance.
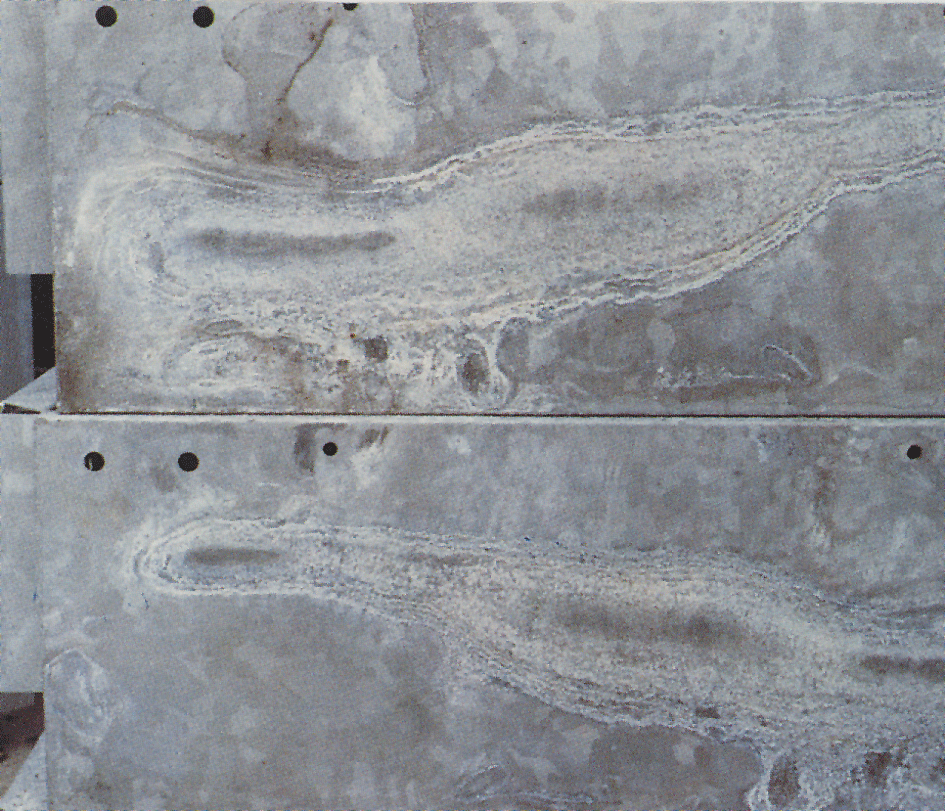
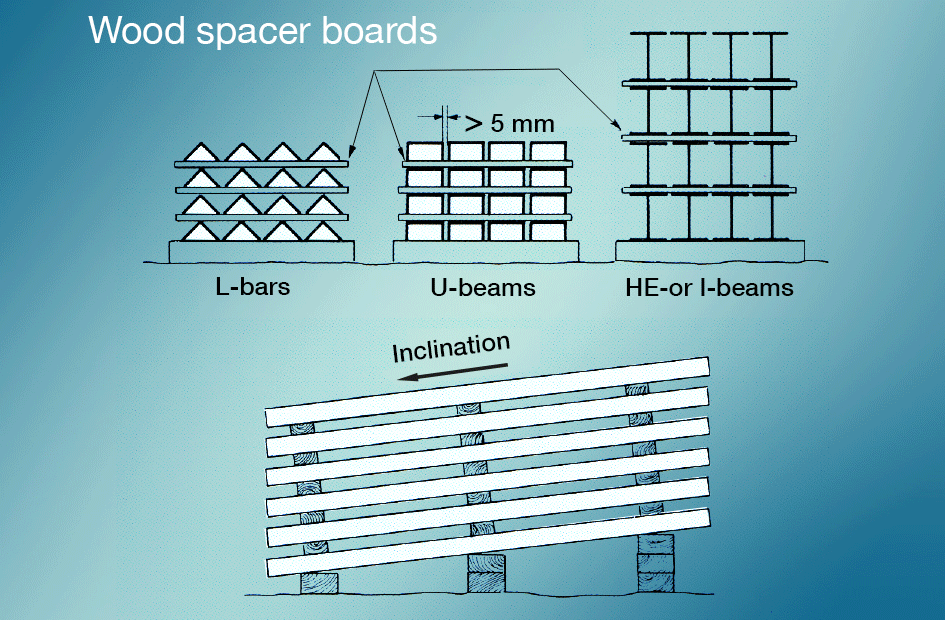
Wet-storage stain is best avoided by preventing newly galvanized surfaces from coming into contact with rain or condensate during transportation. Materials stored outdoors should be stacked so that water can run off easily and so that all surfaces are well ventilated (fig. 5). Painting after galvanizing gives very good protection.
Corrosion in soil
The corrosion conditions in soil are very complicated and variations can be great between different locations, even those in close proximity to each other. Soil can contain weathered products, free or bound salts, acids and alkalis, mixtures of organic substances, oxidizing or reducing fungi, micro- organisms etc. Depending on its structure, soil has different degrees of permeability to air and moisture. Normally, the oxygen content is less than in air, while the carbon dioxide content is higher.
Swedish soils are generally not very aggressive. Average corrosion for zinc is usually taken as 5 µm per year. Severely aggressive soils are seldom seen. In north and west Bothnia, soils may contain sulphur. They are often black, but lighten when exposed to air. In these soils, zinc corrosion rates are very high.
One method of determining the corrosiveness of a soil is to measure its resistivity. If the resitivity of the soil cannot be determined, the rules-of-thumb listed in figure 6 can give a measure of guidance. Where the exposure of metals to soil is concerned, however, it is advisable to seek expert advice from suitably qualified sources.
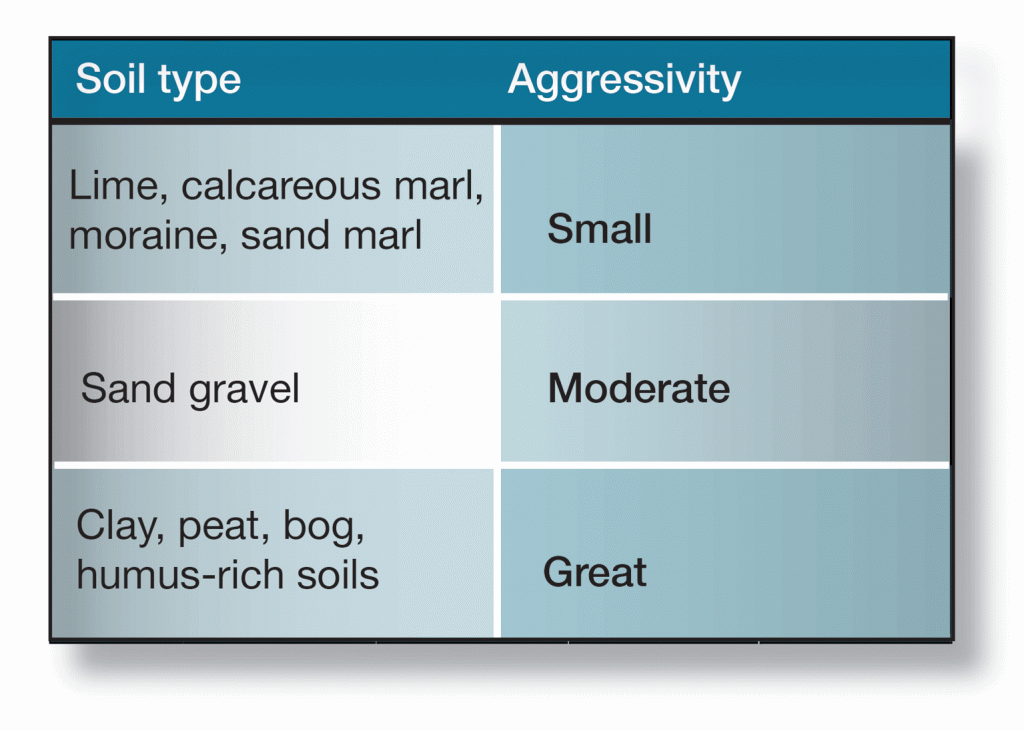
Galvanic corrosion
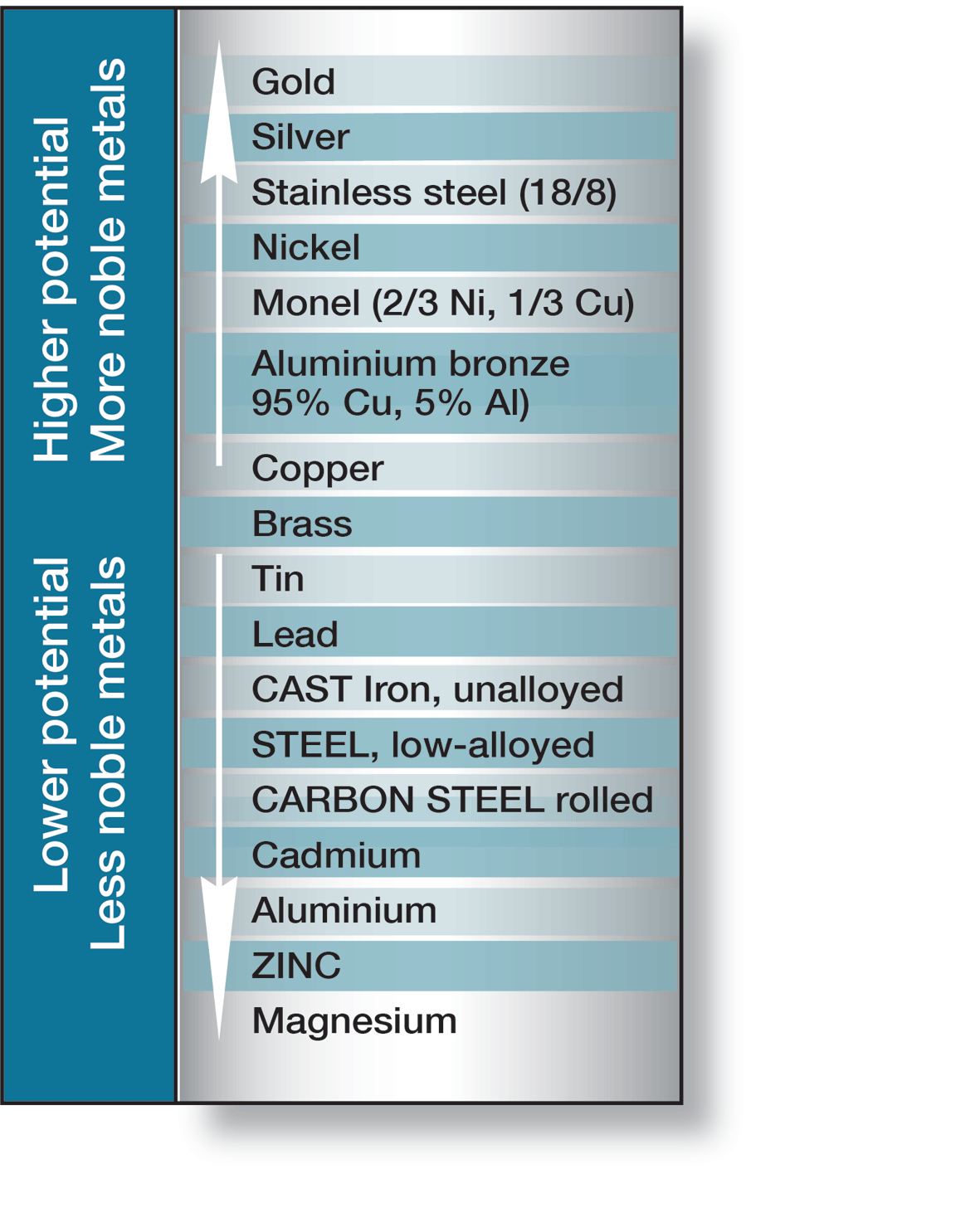
If two different metals or alloys, completely or partially surrounded by an electrolyte, are connected a galvanic cell is created. Which metal becomes the anode or cathode is determined by their electrode potentials in the electrolyte in question. In sea water, which corresponds to the majority of practical conditions, some metals and alloys take up different positions on the electrochemical scale, shown in figure 7.
If steel is connected to copper or brass, the steel becomes the anode in the cell and corrodes. However, if steel is connected to cadmium, aluminium, zinc or magnesium, it becomes the cathode and is protected against corrosion, while the anode metal is consumed. Galvanic corrosion is also called bimetallic corrosion and is used to protect underwater structures from corrosion, when it is termed cathodic protection.
Cathodic protection afforded by zinc coatings
In hot-dip galvanized steel, zinc and steel are in good electrical contact with each other. If the zinc coating is damaged in the presence of an electrolyte a galvanic cell is created. The electrolyte could be condensate or rain water. Sometimes the entire structure can be submerged in liquid. In this cell the zinc becomes the anode or dissolving pole, the exposed steel becomes the cathode and is therefore protected from corrosion.
In the initial phase it is often possible to see a weak ust formation on the exposed part of the steel surface where the coating has been damaged, but after a while whitish-grey areas form which gradually spread over the entire damaged area. The zinc coating corrodes and sparingly soluble zinc alloys descend to the cathode surface where they protect the steel from continued rust attack. This is often called “self-healing”, which is something of a misnomer since the zinc layer is, of course, not restored.
Owing to the cathodic protection generated by the zinc, rust cannot “creep in” under the coating at the point of damage in the way that it can creep under films of paint or coatings of metals more noble than steel. Zinc coatings on steel are unusual, since a fairly large area of damage to the coating does not cause catastrophic loss of rust protection. The range of cathodic protection is dependent on the nature of the electrolyte that creates the cell. For structures in normal atmospheres it is usual to expect protective action over several millimetres. However, in sea water significantly greater distances can be expected.
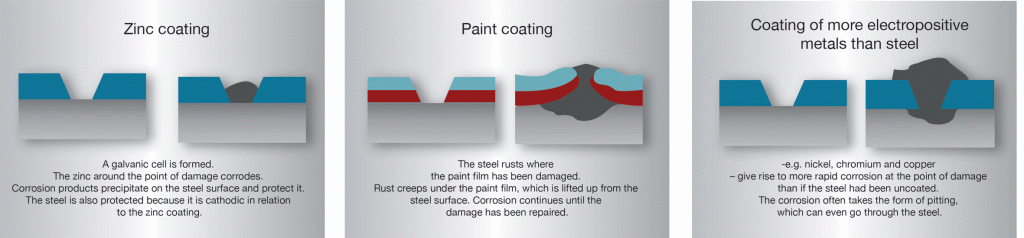
Zinc coatings in contact with non-ferrous metals
The Electrochemical potential scale shows that zinc is less noble than most common metals. This means that when zinc is connected to these metals in a galvanic cell it is the zinc that becomes the dissolving pole. In principle, therefore, such connections should be avoided when possible. A good method is to use an insulator such as plastic or rubber at the joint.
Aluminium and stainless steel can often be connected directly to galvanized material in air or fairly dry environments without noticeable corrosion taking place. However, in water an insulator should always be used.
Copper and copper alloys are more electrically active and there is often a release of copper ions which spread over large surfaces and cause noticeable attack. For this reason, these metals should never be allowed to come into contact with galvanized steel and an insulator should be used.
Hot-dip galvanized steel in contact with mortar, plaster and wood
Damp mortar and plaster attack zinc. The attack ceases when the material dries out. Dry or moderately damp wood, both impregnated and unimpregnated, can be nailed with hot-dip galvanized nails to good effect. However, in the case of nails or threaded unions that are constantly exposed to water an acid-resistant material is preferred. Other dry building materials, such as mineral wool, do not attack zinc.
Packing and transportation of galvanized steel
Even though a hot-dip galvanized coating is capable of withstanding fairly rough treatment it should be handled with care during storage and transportation. In case of long goods simple packing and binding into bundles not only protects against mechanical damage but it often facilitates transportation itself. However, packing and binding should be done in such a way as to avoid risk of wet storage strain. Spacers should be used to prevent such attacks.